-
iestinstrument
CATL Launches the Bedrock Chassis Capable of Withstanding 120 km/h Impact Without Catching Fire Or Exploding
On December 24th, CATL officially launched the CATL Bedrock Chassis, the world’s first ultra-safe skateboard chassis. With its outstanding performance of withstanding 120 km/h frontal impact without catching fire or exploding, CATL’s Bedrock Chassis sets a new standard for intelligent chassis safety, providing comprehensive protection across all scenarios and speed ranges.
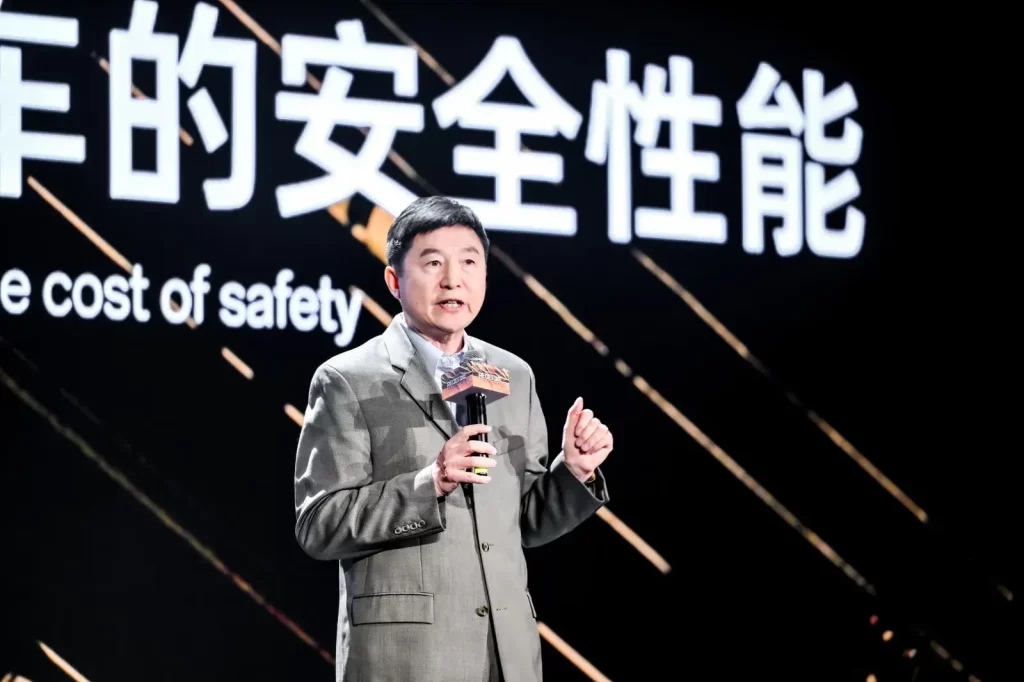
1. CATL Creates a Safer Future with Bedrock Chassis Technology
CATL’s Bedrock Chassis adopts a battery-centered design, using Cell-to-Chassis integration technology to integrate the battery cells directly into the chassis, thus realizing a shared structural design between the battery cells and the chassis. Based on the separation of the chassis from the upper body, the Bedrock chassis is capable of absorbing 85% of the vehicle’s collision energy (compared to 60% for conventional chassis).
Through a number of technological breakthroughs, the Bedrock chassis successfully passed the world’s first “highest speed + strongest impact” double limit safety test, so that the chassis did not catch fire, explode, or hot runway in the 120km/h frontal center column collision test, which redefines the industry’s safety benchmark.
At present, the commonly used C-NCAP (China New Car Assessment Program) frontal collision safety test speed is 56km/h. A frontal collision at this speed generates collision energy equivalent to falling from a 12-meter-high building; a 120km/h frontal collision is equivalent to falling from a 56-meter-high building, generating a collision energy that is 4.6 times that of a 56km/h collision.
In the more rigorous frontal column collision test, which simulates collisions with non-standard objects such as utility poles, large trees and animals, the collision area is only one-sixth that of a full-width frontal collision, and the impact pressure increases exponentially. At 120 km/h, the impact pressure per unit area of the chassis in a frontal center column collision is 21 times that of a full-width frontal collision at 56 km/h in the C-NCAP test.
Due to the extremely high speed and intensity of the collision, no new energy vehicle has dared to challenge the 120km/h frontal column collision test before, and the bedrock chassis of NDT has opened up a new path for the industry in this extreme challenge.
2. Continuous Innovation Drives Advances in EV Safety
CATL Bedrock Chassis carries out in-depth exploration in the field of structural and material innovation, utilizing three major technological breakthroughs to provide unparalleled protection in the full range of scenarios and speeds to ensure the rock-solid safety of the entire vehicle.
The CATL Bedrock Chassis introduces a revolutionary three-dimensional biomimetic tortoise shell structure, where the body and energy unit framework are integrated, deeply coupled to provide the energy unit with indestructible protection. And its aircraft carrier-grade arresting structure disperses impact forces across multiple pathways during a crash, gradually decelerating the vehicle and significantly reducing the depth and speed at which obstacles intrude the cabin. The utilization of submarine-grade hot-formed steel with a strength of 2000MPa, aerospace-grade aluminum alloy with a strength of 600MPa, and multiple barrier structures further enhance the chassis’ rigidity, making it virtually impervious.
In addition, CATL Bedrock Chassis integrates ultra-safe electric core design, NP technology, high ductility energy-absorbing insulating film and other technologies, which breakthroughly leads the industry; in terms of high-voltage disconnection, it realizes the instantaneous disconnection of high-voltage circuits within 0.01 seconds after impact, and completes the residual high-voltage energy discharge in the vehicle within 0.2 seconds, which creates a new record in the industry.
It is worth mentioning that the battery cell has gone through stringent tests, including 60 km/h high-speed sled impact test, 90-degree bending test, and breakthrough sawing test, and the battery did not catch fire and explode in any of the three tests, which are the first of their kind in the industry for CATL, and elevate the safety standard of the battery cell to a new height.
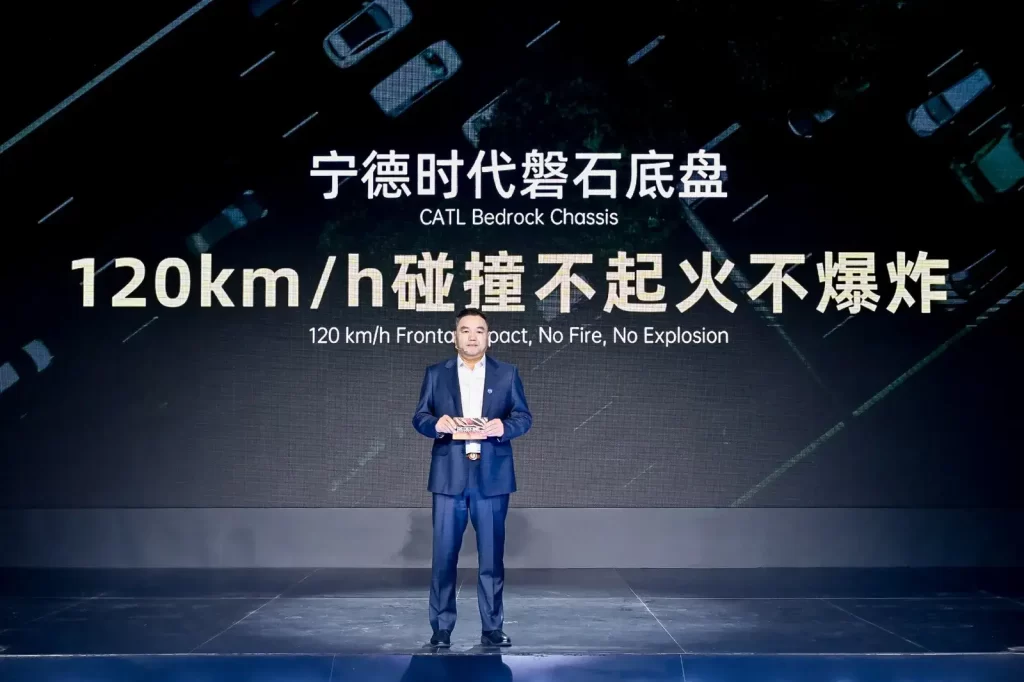
3. Unlocking the era of customization, and activating a trillion-yuan market
The launch of the Bedrock Chassis not only redefines the standard for intelligent chassis safety but also activates a trillion-yuan market. It greatly accelerates the shift towards modular, personalized, and intelligent automotive design.
Addressing the common pain points of high investment, long development cycles, and accelerated product iteration in the industry, the Bedrock Chassis incorporates three core characteristics: internal integration, decoupling of the chassis from the upper body, and external openness. With a rich array of toolkits and solution packages, it offers a scalable software and hardware architecture and standardized interfaces, enabling flexible configurations for different vehicle models and scenarios. This allows the realization of a “one chassis architecture, multiple vehicle models” concept and significantly improves development efficiency and shortens the R&D cycle. The time required for mass production of a vehicle is reduced from the traditional 36 months or longer to 12 to 18 months.
Furthermore, the Bedrock Chassis breaks the limits of safety and modeling, and expands design flexibility through the design of decoupling of the chassis from the upper body. The fourth-generation Cell-to-Chassis (CTC) technology and inverted battery cell technology enhance the utilization of chassis space while reducing the risk of chassis scraping. Additionally, in terms of intelligence, the chassis supports mechanical decoupling, software decoupling and EE decoupling, enabling L3 to L4 intelligent driving capabilities. It provides high adaptability interfaces and promotes collaborative intelligent applications.
Safety is a never-ending journey. In the future, CATL will continue to break technological barriers through continuous innovation, and work with partners to build a safe ecosystem for EV batteries and vehicles, safeguarding the safety of users.
Lithium Battery Testing Solutions Recommend:IEST Instrument
IEST is a high-tech enterprise focusing on R&D and production of lithium ion battery tester. IEST is a professional manufacturer that integrating laboratory instrument R&D and production, method development, instrument sales and technical services. Committed to providing leading testing solutions and services for the global new energy field, IEST company serves key clients like CATL, BYD, Huawei, Svolt, GM, Leyden, Sintef, Factorial, Cabot, Cuberg.
Subscribe Us
Contact Us
If you are interested in our products and want to know more details, please leave a message here, we will reply you as soon as we can.