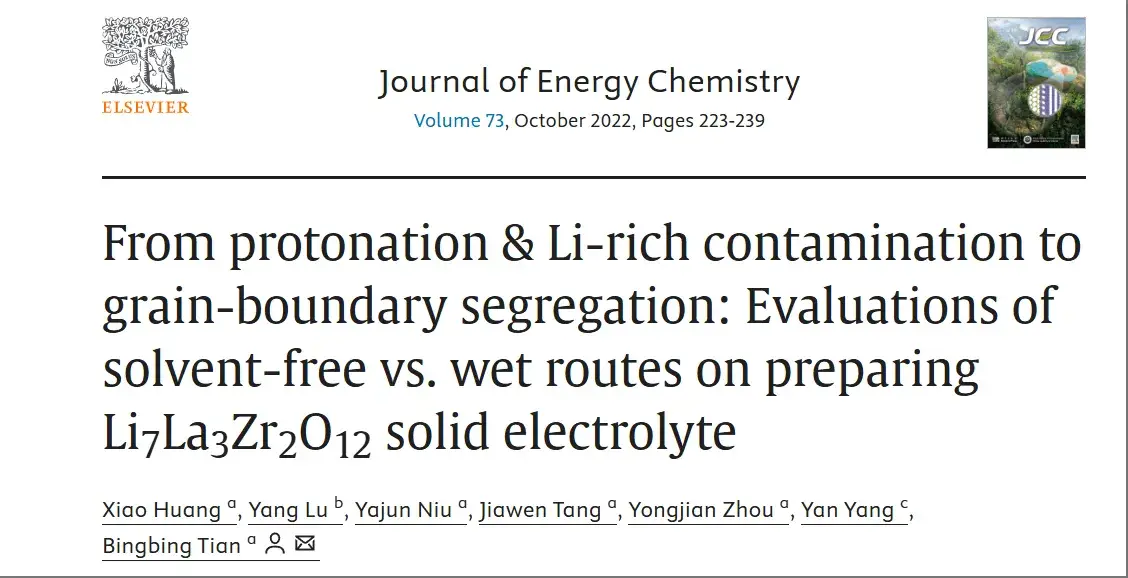
1. Research Background
Metallic lithium, with its exceptionally high specific capacity (3,860 mAh g⁻¹), has garnered intense interest for next‑generation batteries. Solid‑state lithium batteries (SSLBs), by virtue of their safety and potential energy‑density advantages, are strong contenders to replace commercial liquid‑electrolyte Li‑ion batteries (LiBs). Among oxide solid electrolytes, the garnet‑structured Li₇La₃Zr₂O₁₂ (LLZO) is a leading candidate for lithium‑metal SSLBs due to its electrochemical stability against Li metal and high Li‑ion conductivity.
Conventionally, LLZO is synthesized via a wet route using isopropanol (IPA) as the dispersion solvent. However, IPA‑borne moisture can trigger proton–lithium exchange and Li‑enriched surface contamination during mixing and forming, degrading LLZO performance. To mitigate these issues, Dr. Xiao Huang and colleagues developed a solvent‑free process employing hydrophobic polytetrafluoroethylene (PTFE) and polyurethane (PU) binders. They then conducted a systematic comparison—orthogonal evaluation—of wet vs. dry mixing and forming methods, examining microstructure, phase purity, ionic/electronic conductivity, and electrochemical performance.
2. Experimental Scheme
As illustrated in Figure 1, starting reagents LiOH·H₂O, La₂O₃, Ta₂O₅, and ZrO₂ were combined under four process variants:
- 1WW – Wet mixing × Wet forming
- 2WD – Wet mixing × Dry forming
- 3DW – Dry mixing × Wet forming
- 4DD – Dry mixing × Dry forming
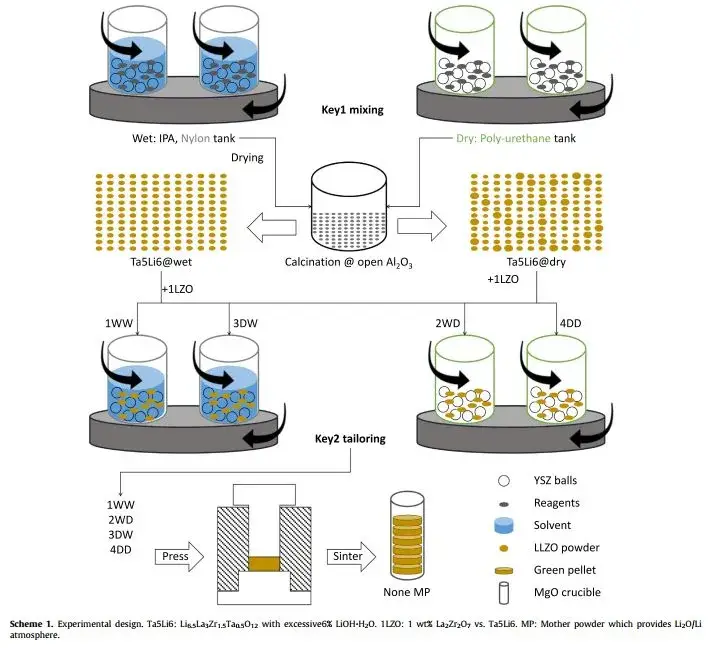
Figure 1. Orthogonal experimental design for LLZO preparation.
Table 1. LLZO preparation parameters
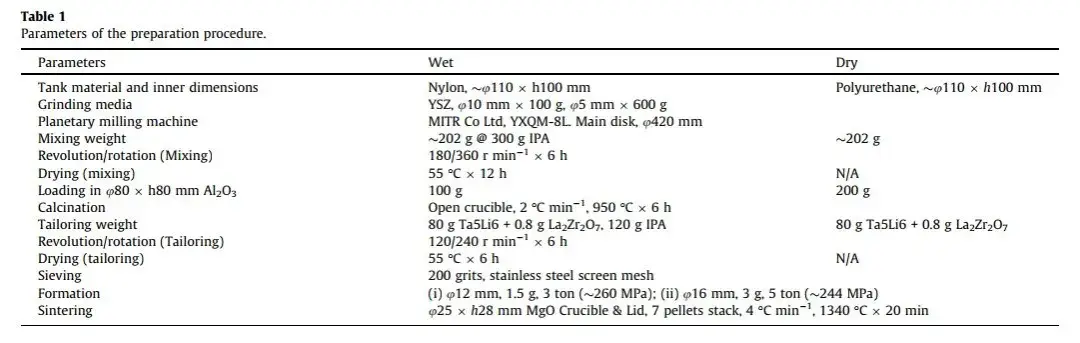
Detailed process parameters are listed in Table 1. The resulting powders were characterized by laser particle sizing, SEM/EDS morphology, and phase analysis. Ionic conductivity was measured with a Toyo LN‑Z2‑HF impedance spectrometer across –55 °C to 25 °C. Li-Li symmetric cells were used for long‑term cycling and critical current density (CCD) tests.
3. Results & Characterization
3.1 Powder Morphology & Surface Chemistry
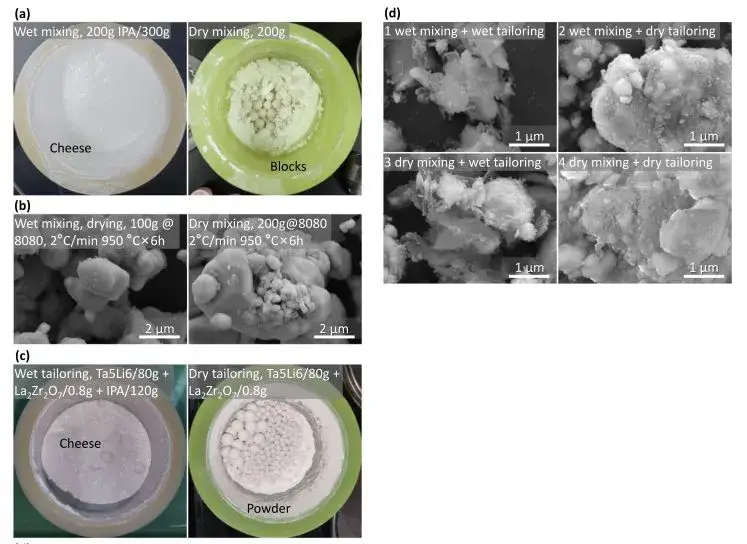
Figure 2. LLZO preparation process.
The slurry prepared by the wet method using IPA as the solvent exhibited a viscous, cheese-like consistency, resulting in increased processing difficulty. However, the sintered particles showed smaller sizes, better uniformity, and lower tap density. In contrast, dry-mixed powders displayed a flaky structure with larger particles and poorer mixing homogeneity. After sintering, the dry-method powders exhibited larger particle sizes and a tap density twice that of wet-method samples. Particle size distribution tests (Figure 3a) revealed that the as-calcined Ta₅Li₆ powders from wet and dry methods aligned with the morphological observations in Figure 2(b). The trimodal distributions of wet-method samples (1WW and 3DW) matched the SEM-derived morphologies, while the unimodal distributions of dry-method samples (2WD and 4DD) deviated significantly from their actual morphologies. SEM images further demonstrated that wet-method LLZO particles were surrounded by flaky impurities, whereas dry-method powders had cleaner surfaces. This indicates that dry-method samples exhibited significantly reduced protonation compared to the severe surface contamination observed in wet-method counterparts. In summary, the wet method offers advantages in mixing and forming uniformity, effectively reducing particle size due to IPA’s solvent support. The dry method, however, requires less time, simplifies processing, and achieves double the tap density of wet-method powders.
3.2 Phase Analysis (XRD)
From XRD patterns, the calcined Ta₅Li₆ powders were primarily composed of the cubic LLZO phase. However, dry-method samples contained detectable tetragonal phases and La₂O₃ impurities, with XRD peak intensities decreasing more significantly than those of wet-method samples. This may correlate with the broadening of full width at half maximum (FWHM) and the degree of particle amorphization. The solvent’s wetting and grinding media in the wet method induced soft lithium-rich contamination at LLZO particle interfaces. In contrast, the solvent-free dry method effectively disrupted the LLZO lattice. Additionally, the c-LLZO lattice expanded significantly after wet-method grinding, primarily attributed to protonation. Dry-method routes resulted in minimal lattice expansion, likely due to the amorphization of LLZO particles.
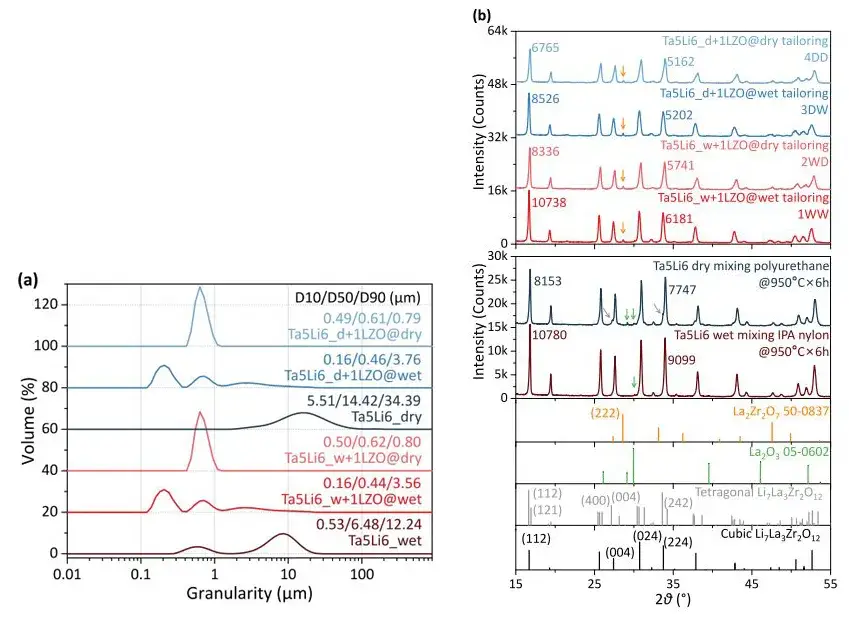
Figure 3. Experimental particle size results and XRD test results
Table 2. XRD quantitative phase analysis
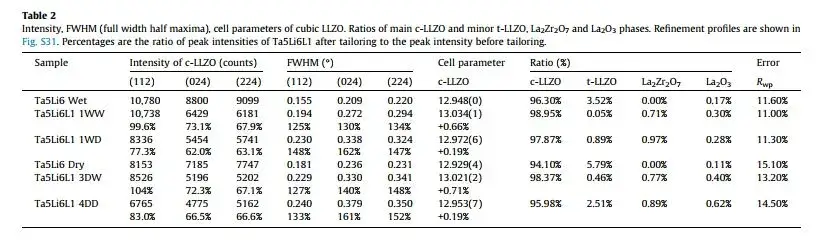
3.3 Protonation and Contamination
FTIR and TG-DSC (Figure 4) demonstrated higher weight loss in wet-formed samples (1WW, 3DW) compared to dry methods (2WD, 4DD), confirming severe protonation in solvent-based routes. SEM cross-sections of wet-method pellets revealed visible contaminants, absent in dry-method samples.
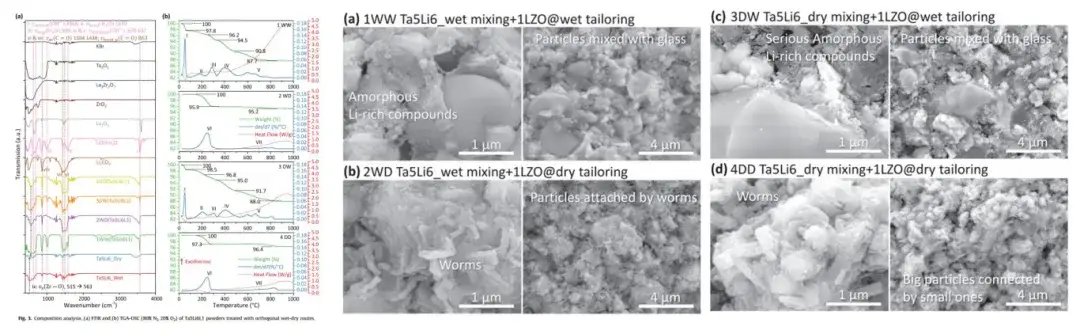
Figure 4. FTIR, TG and SEM results
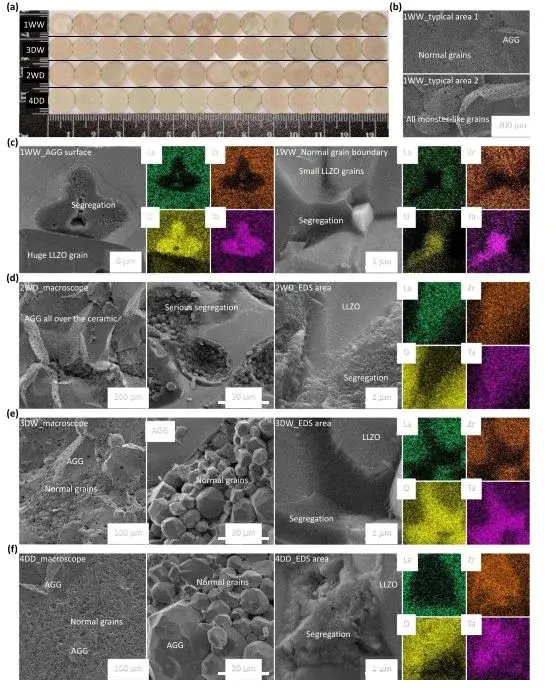
Figure 5. Ceramic sheet and SEM-EDS test results
3.4 Ionic Conductivity and Activation Energy
High-frequency impedance testing from 100 MHz to 1 kHz was employed to measure the ionic resistance of samples at various temperatures. The grain boundary resistance, calculated from the distribution of relaxation times (DRT) results, was fitted and used to determine the activation energy in two temperature ranges: -55°C to 25°C (low-temperature region) and -15°C to 25°C (mid-temperature region). The activation energy data revealed that the interfaces of 1WW, 2WD, 3DW, and 4DD samples exhibited activation energies of approximately 0.3 eV. Such low activation energy values indicate extremely fast lithium-ion transport between the Li anode and LLZO solid electrolyte. Notably, the activation energies obtained in this study are higher than those previously reported in literature, which is primarily attributed to the limited testing frequencies (<1 MHz) of earlier equipment, resulting in underestimated values. This demonstrates that the impedance testing frequency significantly impacts the accuracy of ionic conductivity and activation energy measurements.
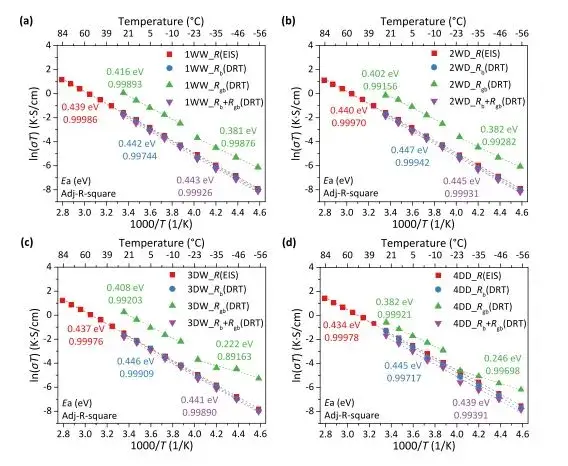
Figure 7. Activation energy test results
3.5 Li-Li Symmetric‑Cell Performance
As shown in Figure 8, under long‑term cycling at 0.1 mA cm⁻² current density and 0.1 mAh cm⁻² areal capacity, the polarization voltage of all four ceramics (1WW, 2WD, 3DW, and 4DD) increased only marginally over 2,000 hours, demonstrating stable interfaces with the Li metal anode and no side reactions. In critical current density (CCD) tests at 60 °C, the 4DD sample sustained a high CCD of 1.6 mA cm⁻² at an areal capacity of 1.6 mAh cm⁻², whereas the other three formulations short‑circuited at 1.1–1.2 mA cm⁻².
Figure 8. Li-Li symmetric long cycle and limiting current density test
4. Summary
As shown in Figure 9, this study compares the process differences between the IPA‑based wet method and the solvent‑free dry mixing method for LLZO preparation. The wet process causes severe surface protonation contamination, whereas the dry route, despite its poorer mixing uniformity during milling, significantly reduces protonation and side reactions, facilitating ceramic sintering and delivering excellent performance. Additionally, the dry method substantially lowers both processing time and cost, providing an efficient and eco‑friendly strategy for industrial production of LLZO powders and ceramics.
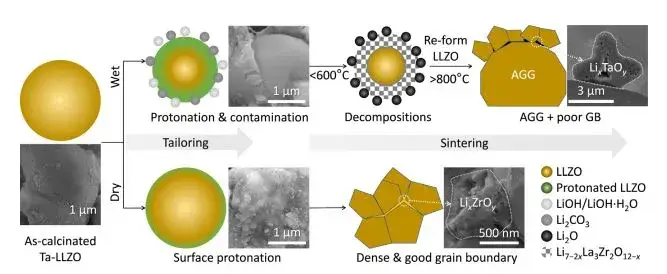
Figure 9. Changes in the molding process of different preparation processes
5. Solid Electrolyte Testing Insights
In the measurement of ionic conductivity for solid electrolytes, an alternating electric field is typically applied to the electrolyte. Under this field perturbation, Li⁺ ions migrate within the grains, leading to the accumulation of cathode and anode charges on either side of the grain boundaries, thereby forming an electrical double layer. By applying sinusoidal AC signals at varying frequencies, the impedance of the solid electrolyte can be determined across different frequencies due to the interplay of resistive and capacitive effects.
For solid electrolytes, distinguishing between grain and grain boundary impedance contributions requires testing frequencies exceeding 7 MHz. However, at frequencies above 7 MHz, parasitic resistance and inductance from instrument circuitry and connections significantly distort measurement results. Consequently, commercially available electrochemical workstations rarely support frequencies above 7 MHz.
Building on this, IEST Instrument offers an ultra–high‑frequency impedance measurement system that, thanks to optimized circuitry, can perform impedance tests up to 100 MHz over a wide temperature range from 90 K (–183 °C) to 873 K (600 °C). This system enables the separation of grain and grain‑boundary impedance in solid electrolytes and other materials for independent characterization, and it also allows calculation of the ionic‑transport activation energy.
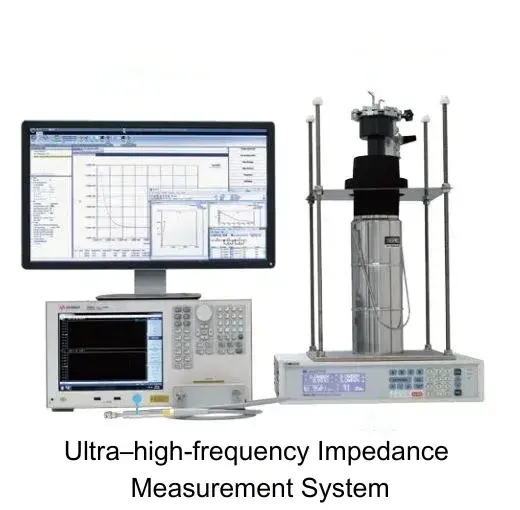
Additionally, IEST Instrument has pioneered a multifunctional Solid Electrolyte Test System(SEMS Series) specifically for solid electrolyte samples. This fully automated platform integrates pellet pressing, electrochemical measurement, and data analysis into one unit. Its all‑in‑one design includes a pressure‑application module, an electrochemical test module, a density‑measurement module, and a ceramic‑disc pressing and clamping module. SEMS is suitable for in situ EIS testing of various oxide, sulfide, and polymer electrolytes under different applied pressures.
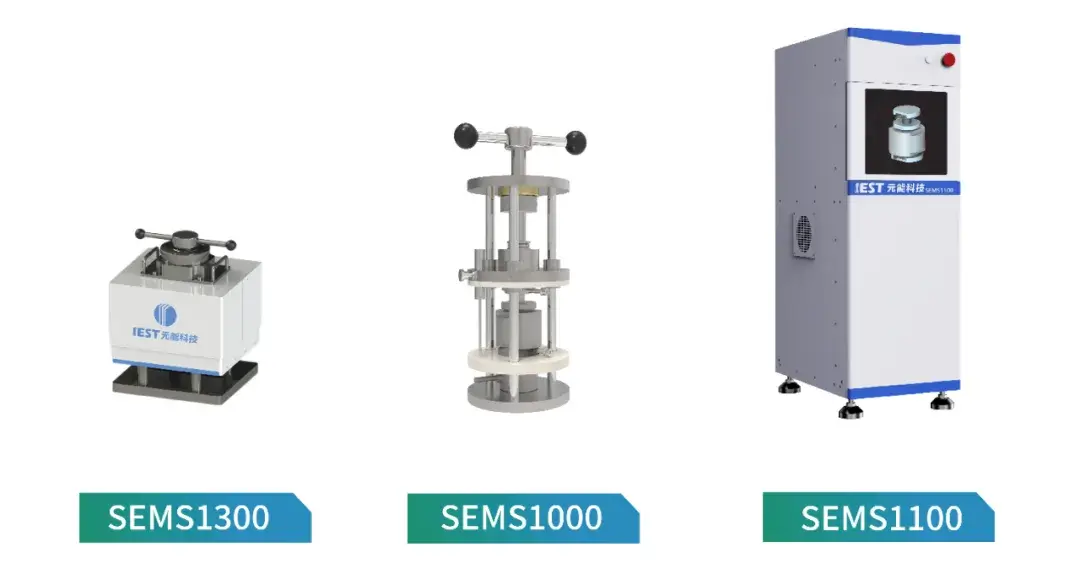