- Home
- Powder Resistivity & Compaction Density Measurement System
- A New Hope for Green Energy: Exploring Dry Electrode Process Technology For Lithium Ion Batteries in 2024
A New Hope for Green Energy: Exploring Dry Electrode Process Technology For Lithium Ion Batteries in 2024
Background:
Dry electrode process technology is shaping the future of green energy solutions, particularly in the realm of Lithium Ion Batteries. In the quest for enhanced energy density, power output, and longevity of batteries, innovative manufacturing processes like dry electrode process technology are gaining momentum. This article delves into the intricacies of dry electrode process and its potential to revolutionize the production and performance of Lithium Ion Batteries.
Lithium-ion batteries dominate new energy power and storage devices due to their high energy density, high power, and long cycle life. As commercial lithium-ion batteries evolve, the industry demands increasingly stringent manufacturing costs and performance. The cost and performance of lithium-ion batteries largely depend on the electrode manufacturing process. Innovative, reliable, and low-cost electrode manufacturing technologies are crucial for promoting the widespread application of lithium batteries. Currently, advanced commercial lithium batteries primarily use a slurry coating method for electrode manufacturing. Figure 1 illustrates the electrode manufacturing process of the slurry coating technique. In this process, slurry preparation involves uniformly dispersing the active powder of the anode or cathode, conductive agents, binders, and additives in a solvent to form a stable suspension. Typically, deionized water is used for the anode, while the organic solvent N-methyl-2-pyrrolidone (NMP) is used for cathode slurry preparation. Coating involves casting the prepared slurry onto the substrate using a slot-die coater, followed by drying in an oven that spans several tens of meters. Drying occurs at high temperatures to rapidly evaporate the solvent. The drying temperature depends on factors such as materials, solvents (water or NMP), and coating speed, and it usually exceeds 100°C, leading to significant energy consumption. Additionally, in cathode manufacturing, due to the potential environmental hazards of NMP, an expensive and complex NMP recovery system is required, further increasing manufacturing costs.
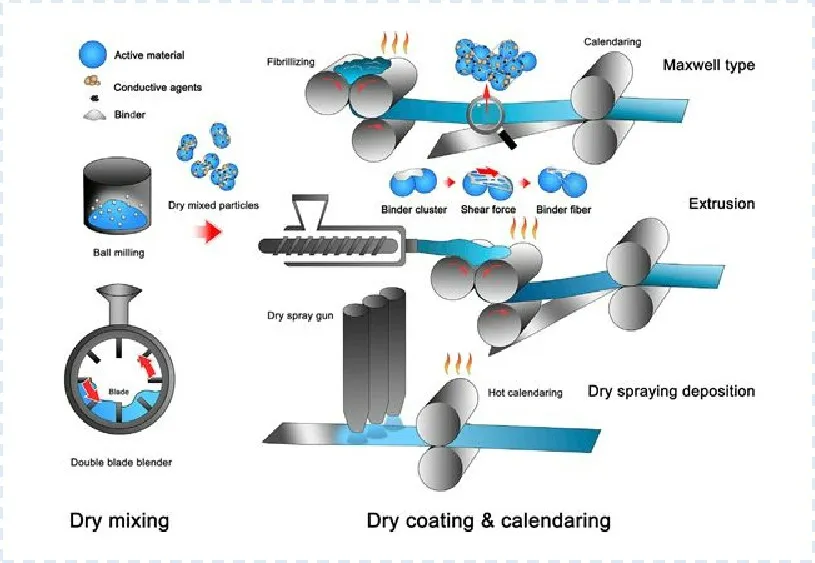
Figure 1. Schematic diagram of the electrode manufacturing process using slurry coating technique
To meet the demand for high energy density, the production of thick electrodes is also a critical development direction. However, the slurry coating process severely limits the manufacture of thick electrodes. The thickness of commercial electrodes is usually less than 100 μm. When using the slurry coating process to produce thick electrodes, the drying process can cause uneven distribution of the binder. If the binder floats to the top of the electrode, it results in a low binder content within the electrode, weakening the cohesion between electrode particles and the adhesion between the electrode and the current collector. This reduced cohesion and adhesion further diminish the mechanical integrity of the electrode, leading to lower yield and decreased production capacity.
Compared to the slurry coating process, dry electrode manufacturing without solvents can potentially avoid all the limitations associated with thick electrode production. In the dry electrode process, the binder, active material, and conductive additives are homogenized in a dry state, preventing uneven binder distribution when producing thick electrodes. Using thicker electrodes can significantly enhance energy density. Additionally, the dry electrode process is increasingly recognized as one of the most promising solutions for reducing manufacturing costs and improving electrode quality.
In summary, the dry electrode process has the following advantages:
1. Cost reduction: Without the need for solvents and related evaporation, recovery, and drying equipment, the dry electrode process can significantly lower production costs. For example, producing one million lithium-ion batteries can save approximately 56% of the cost.
2. Prevention of electrode delamination: The dry electrode process can achieve a uniform distribution of electrode material components without using solvents, thereby avoiding electrode delamination caused by solvent evaporation.
3. Increased active material loading: The dry electrode process is suitable for producing thick electrodes, allowing for better control of electrode thickness and uniformity, which is ideal for preparing ultra-high-loading electrodes.
4.Environmental friendliness: Solvent-free dry electrode technology can effectively reduce environmental pollution.
Over the past five years, Tesla has announced the adoption of the dry electrode process for producing the next generation of batteries.
Volkswagen also claims to have made significant progress in dry electrode technology. The increasing number of patents filed over the past decade indicates a rapid growth in industrial research on dry electrode manufacturing, particularly in dry powder spray deposition and polymer fibrillation methods. The roll-to-roll dry electrode process is currently a primary focus of research. Figure 2 shows the Maxwell dry electrode process flowchart.
Despite the many advantages of the dry electrode process, it also faces some challenges, such as the difficulty in controlling the uniformity and consistency of electrode film formation. These challenges encompass several aspects, including process ratio optimization, adjustment of mixing process parameters, and anomaly detection in the process. Among these, detection is the most challenging part. Ensuring uniformity during the dry electrode film formation process is of utmost importance. This article, based on the detection indicators related to the dry electrode process, outlines IEST current exploration and understanding in the evaluation and detection segment of the dry electrode process.
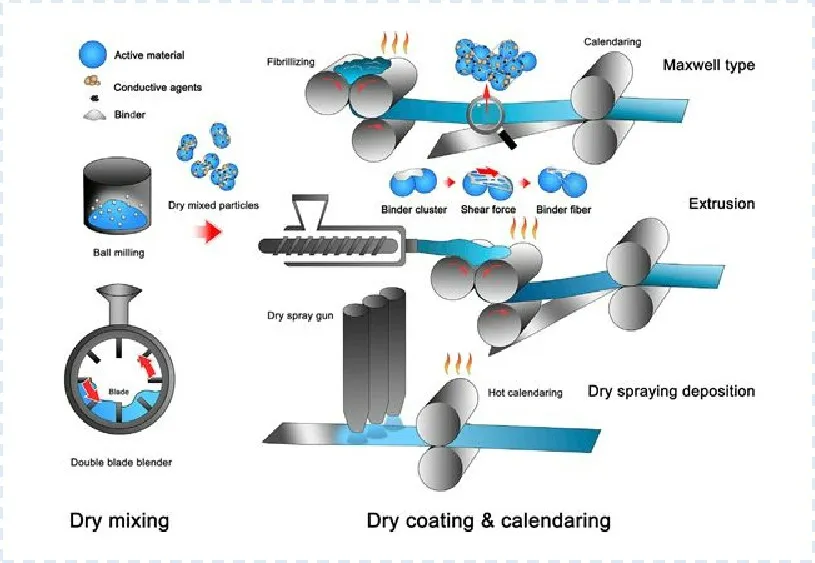
Figure 2. Maxwell dry electrode process flowchart
Evaluation of Dry Electrode Manufacturing Process
Generally, the manufacturing process of roll-to-roll dry electrode typically involves three steps: dry mixing, dry coating (dry deposition), and final pressing, to achieve the desired thickness and dense electrode structure. The uniformity of the dry mixing process is crucial for subsequent processes. Additionally, the process ratio in the dry mixing process ultimately affects the electronic or ionic transport pathways in subsequent processes, the compaction density of the electrode sheets, and even the electrochemical performance indicators of battery cells. The indicators of powder resistivity and compaction density are crucial in current lithium battery research and process evaluation. Figure 3 shows the results of powder resistivity and compaction density determination based on the PRCD series equipment for “dry mixing”. The positive electrode materials, binder, and conductive agent were mixed in different ratios (NCM: PVDF = 19:1 and NCM: PVDF: SP = 18:1:1) to prepare mixed powders of different ratios, aiming to simulate the mixing stage of the dry electrode process. From the results, it is evident that with the introduction of conductive agents and binders, the electrical conductivity and compaction density of the mixed powders exhibit significant differences.
In the dry electrode process, the core material during the dry mixing stage is the binder PTFE, which possesses “fibrillation” capability. It is mixed with active materials and conductive agents to ensure uniform dispersion of various materials during the mixing process. Under the action of shear force, the binder is physically stretched from its original spherical shape into fine fibers (referred to as “fibrillation”). The resulting network structure can interconnect the active particles, thus achieving good bonding. The key focus during this process is the ratio of each material and the process parameters of mixing to ensure uniform dispersion. Introducing monitoring of resistivity and compaction density during the mixing stage can provide effective theoretical support for optimizing process ratios and parameters.
Figure 3: Results of powder resistivity and compaction density determination for “Dry Mixing”
Compared to the material mixing stage in the laboratory, recent laboratory tests on dry electrode samples have shown a direct correlation between the resistivity of mixed powders and the resistance of pressed electrodes. This further emphasizes the significant importance of evaluating the conductivity of mixed powders. Unlike powder testing during the dry mixing stage, testing during dry coating (dry deposition) and final pressing stages primarily focuses on the electrode level. Evaluating the performance at the electrode level is crucial for the final presentation of electrochemical performance. IEST Laboratory systematically evaluates the electronic conductivity performance and ion transport pathways of dry electrodes at the electrode level by combining electrode resistivity and curvature testing.
The evaluation of electronic conductivity performance of dry electrodes described here primarily involves combining the BER series dual-plane controlled compression disc electrode resistance method to evaluate the upper and lower electronic conductivity of the electrodes. This method enables testing the electronic conductivity performance of electrodes/collectors prepared with different positive electrode materials, negative electrode materials, conductive agents, binders, and current collector types during the dry electrode manufacturing process, facilitating process ratio optimization. Additionally, by measuring the electronic conductivity performance at different points on the same electrode, the uniformity of electrode coating can be effectively assessed, providing a direct correlation with uniformity monitoring indicators during the dry electrode manufacturing process. Figure 4 illustrates the evaluation of electrode coating uniformity, and this method can be effectively implemented during both dry coating and final pressing stages for comprehensive testing.
Figure 4. Schematic diagram of electrode coating uniformity evaluation principle
The evaluation of ion transport pathways in electrodes conducted at IEST Laboratory introduces the concept of tortuosity, which represents the degree of bending of the porous electrode transport paths. Tortuosity is another important parameter related to transport characteristics besides porosity. It can be used to characterize the electrolyte’s permeability and the migration rate of ions, thereby affecting the battery’s capacity and rate performance. Dry electrodes have significant advantages in post-coating processes. The electrode thickness is closely related to the effective ion transport path and rate performance. Effective evaluation of electrode-level tortuosity is crucial for predicting post-process electrochemical performance and assessing capacity performance.
Figure 5 illustrates the principle of electrode tortuosity evaluation based on the EIC series equipment. Electrochemical impedance spectroscopy (EIS) measurements are performed on symmetric cells assembled with electrodes, and the ion resistance (Rion) is calculated by combining the impedance values at high and low frequency ranges of the EIS curve. Further evaluation of tortuosity is conducted by incorporating parameters such as electrode area (A), electrolyte conductivity (σ), electrode thickness (d), tortuosity (τ), and MacMullin number (Nm). The introduction of Nm eliminates the need for porosity ε, directly assessing the effective transport pathway of lithium ions based on the MacMullin number concept.
Figure 5. Schematic diagram of electrode tortuosity measurement principle
Summary
Dry electrode manufacturing technology represents a new hope for green energy, offering advantages in both cost and battery performance, with potential applications in other processes such as solid-state batteries and pre-lithiation. However, significant challenges remain in process manufacturing and industrialization.
Researchers in the industry are particularly focused on understanding the bonding mechanism, differences in binder types, long-term cycling performance at the cell level, and stability assessment of the manufacturing process for dry electrodes. In the film formation stage of dry electrode processes, IEST has introduced series equipment such as PRCD, BER, and EIC to evaluate powder and electrode-level performance, aiding in process ratio optimization and process scheme modification.
In addition, for subsequent stages of the film formation process, IEST also conducts evaluations of electrochemical performance analysis, gas generation in cells, and expansion performance testing. These evaluations, along with others, provide new support and insights for scientific research and industrial applications.
References:
[1] Zhang Y, Lu S, Wang Z, et al. Recent technology development in solvent-free electrode fabrication for lithium-ion batteries[J]. Renewable and Sustainable Energy Reviews, 2023.
[2] Landesfeind, Johannes,Hattendorff, et al. Tortuosity Determination of Battery Electrodes and Separators by Impedance Spectroscopy[J].Journal of the Electrochemical Society, 2016.
[3] Juarez-Robles D .Electroanalytical Quantification of Electrolyte Transport Resistance in Porous Electrodes[J].Journal of The Electrochemical Society, 2020, 167(8):080510 (16pp).
Share
If you are interested in our products and want to know more details, please leave a message here, we will reply you as soon as we can.